Beyond Square Meters: Why Bamboo Construction Demands a Custom Approach to Costing
- Oleg Nashchekin
- Feb 6
- 4 min read
Updated: May 29
The question that’s always on everyone’s mind is, “How much will it cost to build?” It’s a perfectly natural inquiry, as having a clear estimate can help clients confidently move forward with their plans. However, answering this question isn't always straightforward, especially when it comes to bamboo construction. Unlike general construction projects, where costs can often be estimated on a per square meter (or foot) basis, bamboo craftsmanship introduces unique complexities. Let’s explore why this is the case.
Why is it challenging to provide a price per square meter for bamboo construction?
The per square meter approach is the default method of estimating costs in general construction, especially for standardized buildings, but it doesn’t translate well to bamboo projects. Here’s why:
1. Supply Chain and Material Availability
In general construction, the cost of materials is relatively easy to estimate because of a well-established supply chain for traditional materials like cement, bricks, steel, etc. Numerous suppliers with readily available stock can meet demand across most regions of a country, ensuring consistency in material pricing.
In contrast, bamboo supply chains are far less developed. There are limited suppliers offering construction-grade bamboo, and even fewer can guarantee that the bamboo is properly treated to ensure durability and safety. Often, sourcing bamboo requires purchasing it directly from farms, plantations, or forests. This means that costs vary significantly depending on factors such as location, availability, transportation, quality, and even the willingness of farmers or landowners to negotiate.
At Kiri Bamboo, we take sourcing seriously. Beyond ensuring the quality and affordability of harvested bamboo, we prioritize sustainable harvesting practices. These practices add complexity and cost but are essential to preserving the environment and ensuring long-term bamboo availability.

2. Complexity of Bamboo Design
Bamboo structures often feature intricate and unique designs, such as complex roofing systems with concave and convex shapes, that are unmatched by other construction methods. While these designs are undeniably stunning, they pose significant challenges when estimating costs. Standard formulas for Euclidean geometry often cannot be applied, making it difficult to calculate areas like roof surfaces accurately without drawings and physical models.
Traditional gable roof design vs. curved concave bamboo roof (Photos by Kiri Bamboo)
For many architects around the globe, bamboo remains a novel material. They must first understand its unique properties and learn how to integrate it with their existing architectural knowledge. Often, this involves traveling abroad to study bamboo architecture and acquire practical, in-field experience. While bamboo architecture offers immense creative possibilities, it also presents critical practical limitations that, if overlooked, can compromise the integrity and durability of the structure. That’s why it’s so valuable to work with already experienced bamboo architects or find willing architects to learn about all the intricacies of bamboo architecture.
As with any creative process, it takes time, research and possibly several iterations to achieve the desired design between architects, engineers, craftsmen and clients. Therefore, the architectural services vary drastically from project to project due to the size, complexity and requirements of bamboo structures.
3. Specialized Skills and Craftsmanship Joinery Choices
Working with bamboo demands a specialized skill set that differs greatly from conventional construction. Craftsmen must be trained and experienced in handling bamboo in its various forms—poles, splits, strips, flattened sheets and other bamboo-made materials—and know how to integrate complementary materials such as wood, clay, cement, or metal when necessary. This expertise contributes to both the timeline and cost of a project.
Depending on the scale, design and budget of any bamboo project, various joinery techniques can be utilized. As a rule, large and heavy structures need more sturdy and complex joints. But more complex joinery for more simple structures also can be considered for aesthetic appeal. The choice of joinery can vary broadly from simple lashing to wedge connections to elegantly carved joins like flute or fish mouth if we are talking about traditional bamboo joint techniques. But there are also more modern methods of joinery like bolted joints or other more advanced types of steel connectors. A single project may feature a combination of these methods to balance strength, appearance, and functionality.
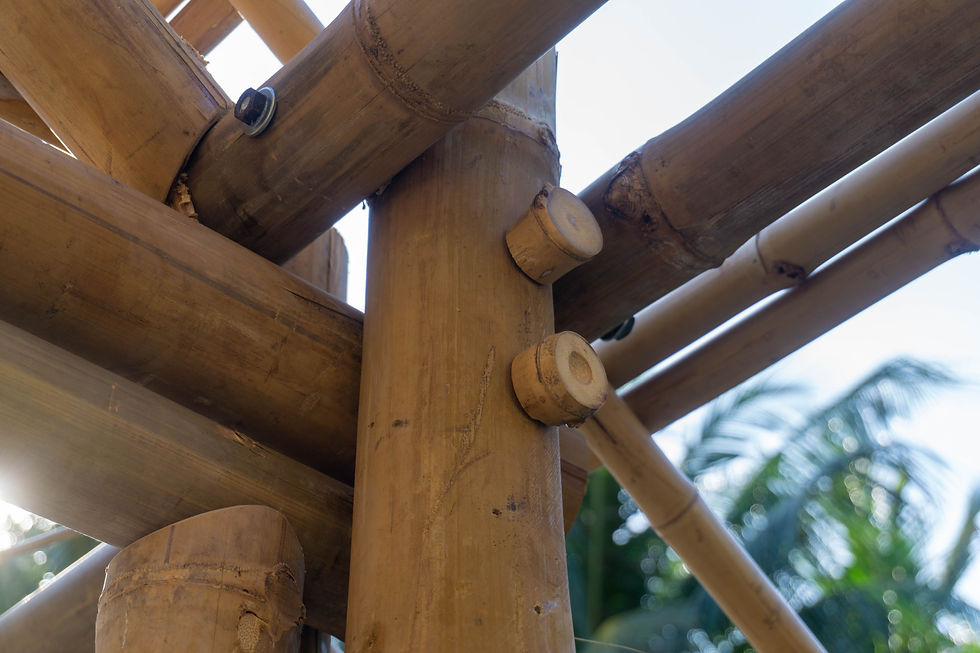
4. Additional Factors Influencing Costs
Several other variables further add to the complexity of cost estimation, including:
Construction Site Location: The terrain, available infrastructure, and accessibility of the site significantly impact costs. Challenging or remote locations often require additional preparation and resources, driving up expenses.
Logistics: Transporting bamboo and other materials to hard-to-reach areas or across long distances can substantially increase costs, especially if specialized vehicles or equipment are required.
Material Choices: The selection of materials plays a crucial role in determining overall costs. Decisions about foundations, roofing materials, walls, finishes, furnishing, and decorative elements all contribute to the final budget.
Business Expenses: As with any business, indirect costs—such as legal and professional services, SG&A expenses, and employee benefits — must be accounted for. Though these may not appear directly on construction quotes, they are essential for the sustainability of any well-functioning enterprise.
Permits and Building Codes: In countries with strict construction regulations, compliance can involve extensive paperwork, inspections, and fees. Navigating these requirements adds both time and cost to the project.
Why a Custom Approach Works Best
Given these challenges, estimating costs using the standard per square calculation method is often impractical for bamboo construction. A more effective approach begins with a professional bamboo architect designing the project based on the client’s specific requirements. These designs are then shared with the craftsmanship team, which creates a small-scale bamboo model to explore structural feasibility and durability of the proposed structure. In addition, the representatives of the craftsmanship team conduct a site visit to assess the terrain, infrastructure, and other local conditions.
By combining the architectural designs, bamboo modeling and site-specific insights, the craftsmanship team can create a detailed, customized estimate for the project. This process ensures greater accuracy, transparency, and alignment with the client’s vision and budget.
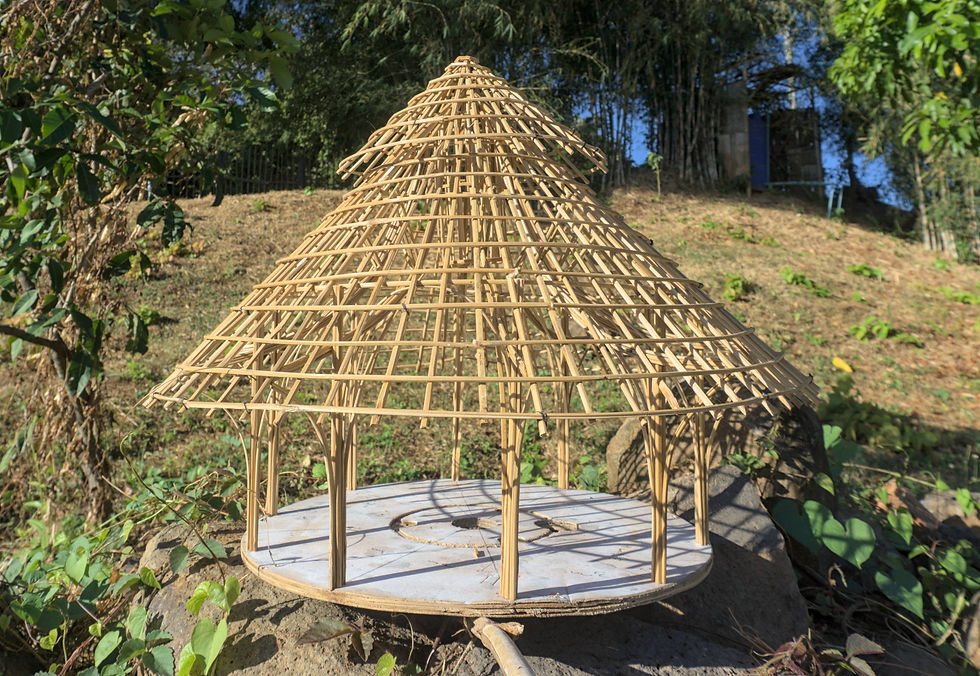
Embrace the Bamboo Difference
Yes, bamboo costs more effort to price—but it also offers what concrete and steel cannot: sustainability, artistry, and a connection to nature. By valuing customization over shortcuts, we build spaces that inspire and endure.
Ready to start your bamboo journey? Contact us for a consultation tailored to your project.
Comments